How Contractors Use 3D Scanning to Minimize Budget Overruns
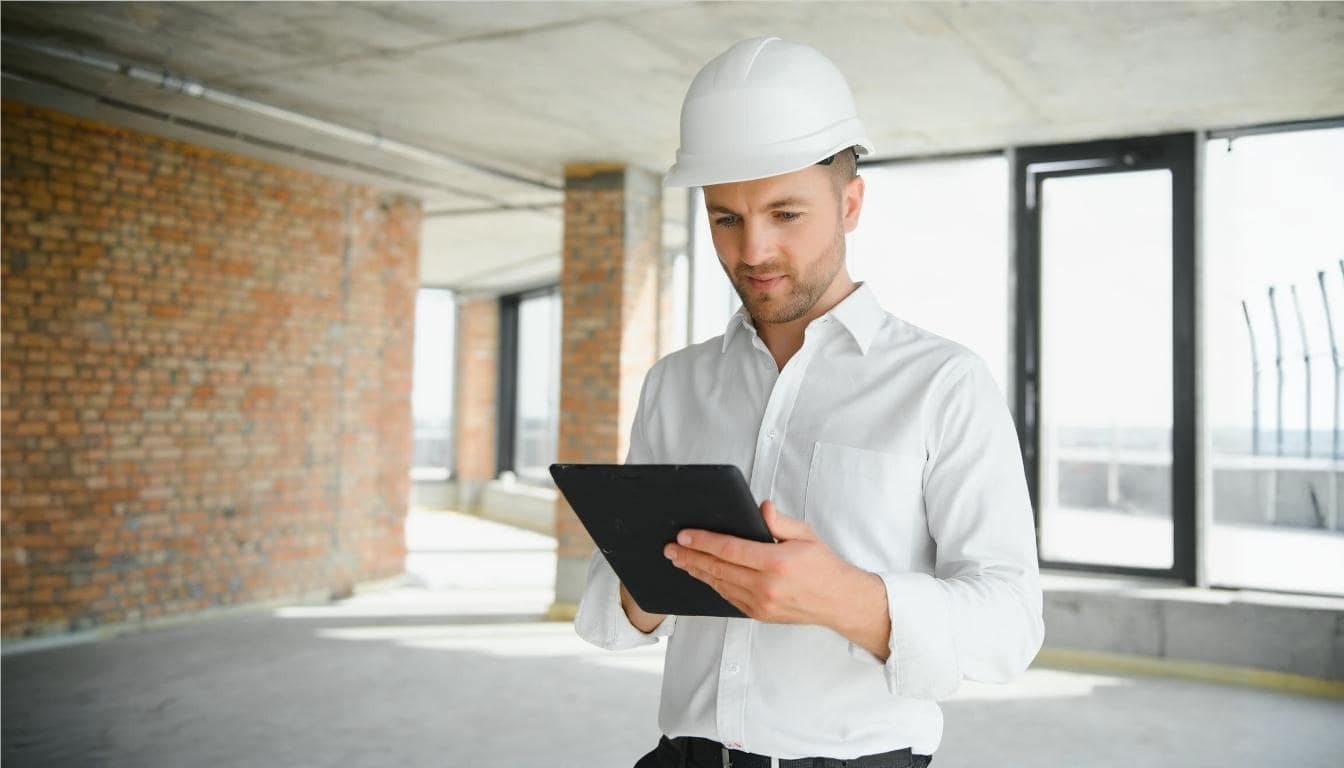
In the world of construction, staying within budget can be a monumental challenge. Unforeseen conditions, miscommunications, and design errors often lead to costly overruns that stress stakeholders and derail projects. Thankfully, advancements in technology, particularly 3D scanning, are revolutionizing the way contractors approach planning, execution, and problem-solving.
Laser scanning technology has revolutionized the way construction professionals manage project costs. From pre-construction planning to as-built documentation, this laser scanning technology allows contractors to work smarter, reduce risks, and ensure projects stay on track financially. Let’s dive into how 3D scanning is transforming the industry and helping contractors minimize budget overruns.
What Is 3D Scanning?
At its core, 3D scanning uses laser technology to capture the precise geometry of a physical space or object, creating a digital representation known as a point cloud. These point clouds can be transformed into 3D models, as-built documentation, or incorporated into Building Information Modeling (BIM) systems.
The accuracy of 3D scanning allows construction professionals to visualize and analyze spaces down to the millimeter, eliminating many of the uncertainties that have traditionally plagued construction projects.
Why Budget Overruns Happen in Construction
Before exploring how 3D scanning addresses budget overruns, it’s important to understand why they occur. Here are a few common culprits:
- Inaccurate Site Data: Traditional surveying methods often leave room for interpretation or miss key details, leading to errors in design and planning.
- Design Changes: As projects evolve, unexpected changes to the original plan can create additional costs.
- Rework: Misplaced components or errors in measurements can lead to expensive corrections during the construction process.
- Poor Communication: Breakdowns in coordination among architects, engineers, and contractors can cause confusion and project delays.
- Unforeseen Conditions: Especially in renovation or retrofit projects, hidden conditions like structural issues or mismarked utilities can lead to major setbacks.
By addressing these issues head-on, 3D scanning helps contractors mitigate risks and avoid financial pitfalls.
Applications of 3D Scanning in Construction
1. Pre-Construction Planning
One of the most impactful ways 3D scanning reduces budget overruns is during the pre-construction phase. By providing detailed and accurate site data, 3D scanning enables contractors to:
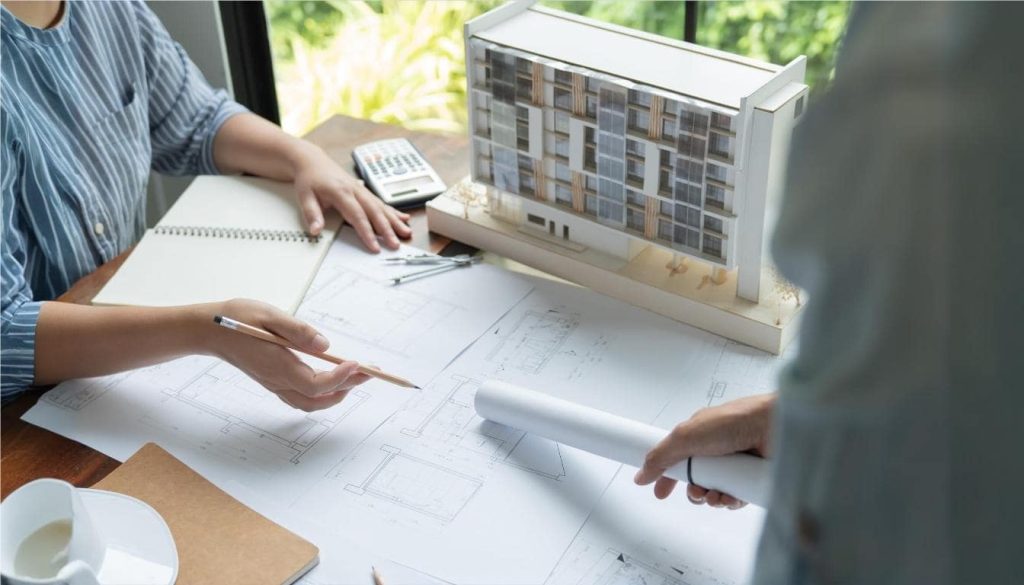
- Perform precise site analysis.
- Pinpoint potential issues, like uneven ground or structural misalignments, prior to starting construction.
- Collaborate effectively with architects and engineers using a shared, detailed model.
Accurate data reduces the likelihood of design errors and ensures that all stakeholders are on the same page before the first shovel hits the ground.
2. As-Built Documentation
As-built documentation is essential for capturing the exact state of a project at various stages. 3D scanning creates precise records of existing conditions, ensuring:
- Accurate measurement of existing structures for retrofit or renovation projects.
- Seamless integration of new designs into old spaces.
- A dependable resource for contractors, minimizing the likelihood of expensive errors during implementation.
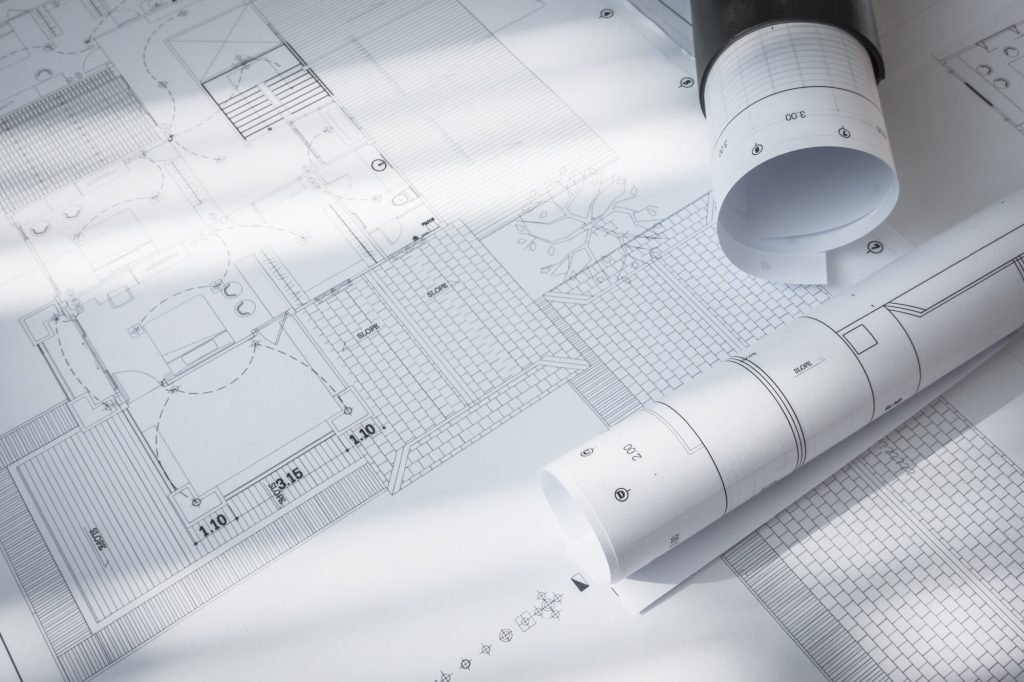
For instance, in tenant improvement projects, as-built documentation allows contractors to navigate complex, pre-existing conditions with confidence, ensuring renovations stay on schedule and budget.
3. BIM Integration
Building Information Modeling (BIM) is a fundamental aspect of contemporary construction, and 3D scanning fits effortlessly into this workflow. By combining point cloud data with BIM software, contractors can:
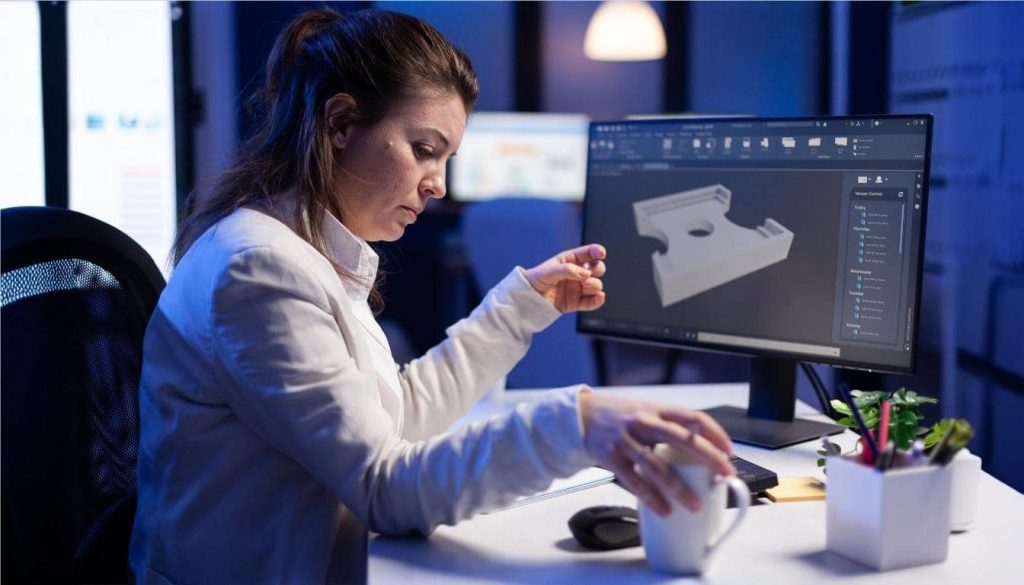
- Create highly accurate, data-rich models of construction projects.
- Model various construction scenarios to detect potential challenges in advance.
- Streamline processes, from acquiring materials to managing project timelines.
BIM integration not only enhances project efficiency but also provides a clear roadmap, reducing the likelihood of surprises and subsequent budget overruns.
The Importance of 3D Scanning in Renovation Work
Renovation projects frequently present a distinct array of challenges. From dealing with outdated infrastructure to adapting to hidden conditions, contractors must navigate the unknown. Here, 3D scanning offers unparalleled advantages.
Tenant Improvement Projects
In commercial and residential renovation projects, as-built documentation is critical for understanding existing layouts. 3D scanning helps contractors:
- Capture detailed measurements of walls, ceilings, floors, and utilities.
- Avoid clashes between new installations and existing structures.
- Plan renovations that align with the client’s budget and timeline.
By providing an accurate starting point, 3D scanning minimizes the risk of costly surprises mid-project.
Real-World Impact: How Contractors Are Benefiting
The adoption of 3D scanning technology is transforming construction workflows by enhancing accuracy, streamlining processes, and reducing unnecessary expenses. Contractors can now rely on precise digital models and comprehensive data to guide every stage of their projects.
Key benefits include the ability to uncover potential structural issues early, improve coordination between teams, and reduce the likelihood of costly errors. By integrating 3D scanning into pre-construction planning, on-site assessments, and documentation, contractors can achieve more predictable project outcomes while staying within budget and on schedule.
This technology enables professionals to make well-informed choices and utilize their resources effectively, leading to more streamlined and successful construction projects.
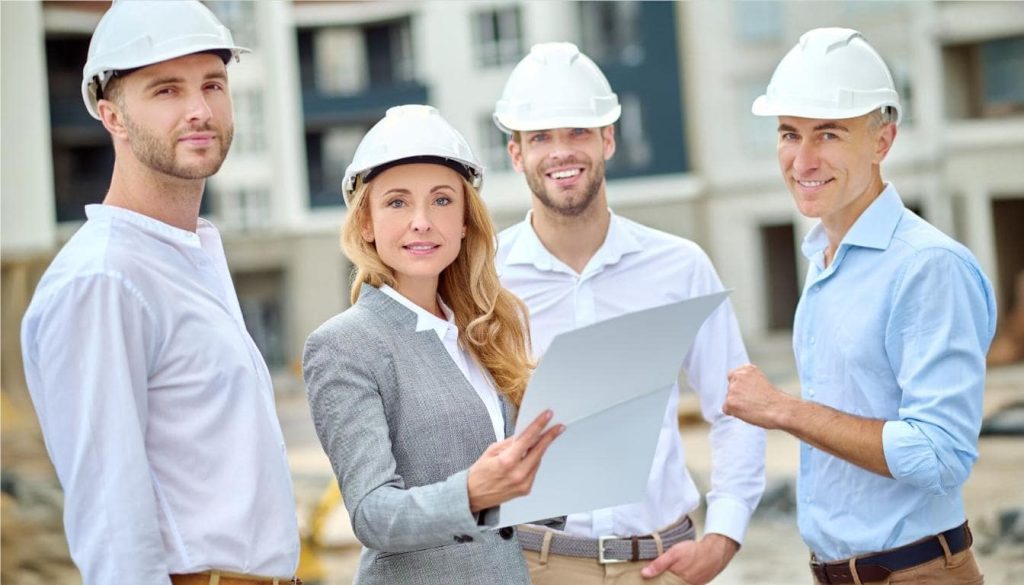
Advantages of 3D Scanning for Cost Management
- Enhanced Accuracy: Laser scanning captures every detail, reducing the likelihood of measurement errors and rework.
- Risk Reduction: By uncovering potential issues early, contractors can address them proactively, avoiding unexpected costs.
- Time Savings: With faster data collection and more efficient planning, projects can move forward more quickly.
- Improved Collaboration: Shared, highly detailed models foster better communication among stakeholders.
Looking Forward: The Evolving Future of 3D Scanning in Construction
With laser scanning technology becoming increasingly accessible, its impact on construction is set to grow significantly. Emerging trends include:
- Drone-Based Scanning: For large or hard-to-reach sites, drones equipped with 3D scanners are streamlining the data collection process.
- Real-Time Scanning: Advances in real-time scanning and augmented reality are enabling contractors to visualize changes on-site instantly.
- AI Integration: Artificial intelligence is now utilized to process 3D scan data, detecting potential problems and offering automated solutions.
These innovations pave the way for enhanced precision, improved efficiency, and greater cost savings for contractors in the future.
Our 3D Models Examples
Conclusion
3D scanning has emerged as a vital tool for contractors looking to minimize budget overruns and improve project outcomes. Offering exceptional precision and practical insights, this technology is reshaping how construction projects are designed, carried out, and recorded. Whether it’s pre-construction planning, as-built documentation, or BIM integration, 3D scanning offers a clear path to smarter, more efficient construction. For contractors in the U.S., embracing this advanced technology has shifted from being optional to essential in today’s competitive and budget-focused industry.