3D Scanning Cost: A Full Guide to 3D Scanning Price in US
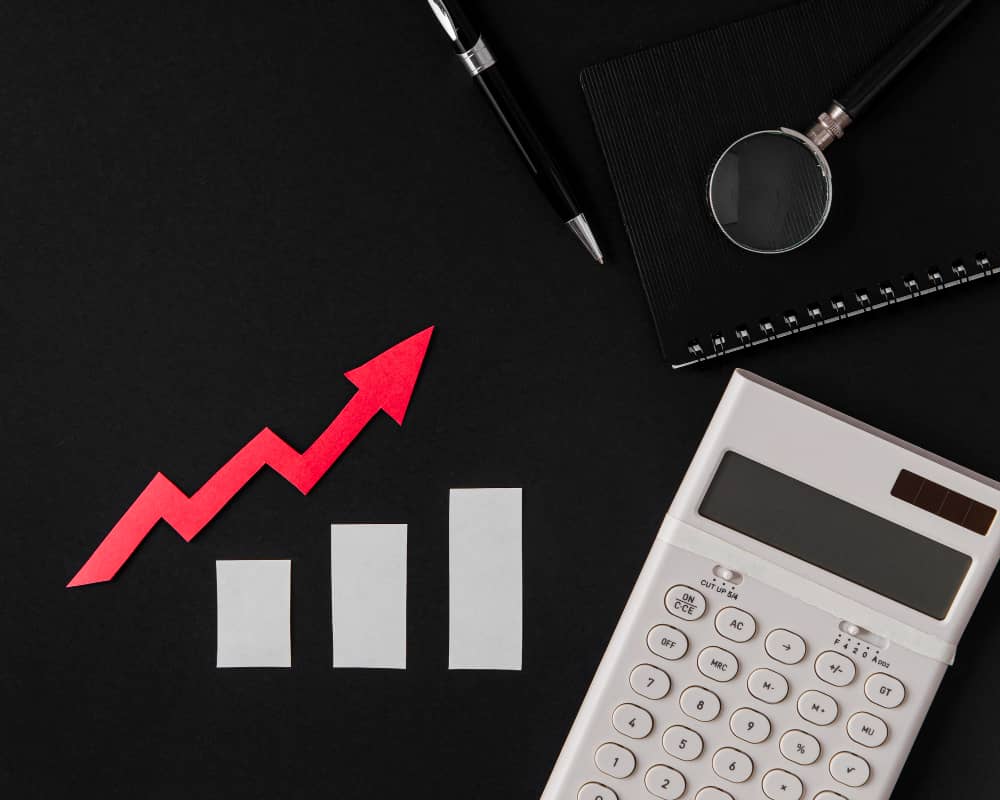
3D scanning has revolutionized the way construction, design, and architectural projects are planned and executed. By capturing precise measurements and creating highly accurate 3D models, the technology provides essential data for various industries. However, understanding the cost of 3D scanning is critical for stakeholders such as architects, engineers, and construction companies. The final cost is influenced by various factors such as project size, complexity, the equipment utilized, and the project’s location.
What is 3D Scanning?
3D scanning is a technique that uses laser technology to precisely capture the geometry and dimensions of a physical object or space. By emitting laser beams across a surface, a scanner records data points to create a digital representation known as a point cloud. This point cloud is then processed into 3D models or 2D drawings, providing invaluable data for architectural projects, reverse engineering, or preserving historical landmarks. The technology’s ability to capture detailed information down to the millimeter ensures that construction plans are executed with the highest precision.
Who Needs 3D Scanning?
Various industries rely on 3D scanning to meet specific needs. Architects and designers use it to accurately document spaces, especially when working with complex structures or when renovation is involved. Construction companies benefit from precise measurements, minimizing errors during the building phase. Real estate developers, too, utilize this technology for efficient space management and documentation.
Additionally, private homeowners or individuals may require 3D scans for small-scale projects such as home renovations or extensions. These scans help ensure that the design process is based on accurate spatial data, reducing the likelihood of costly mistakes during construction.
3D Scanning Services Examples
Why is 3D Scanning Important in Architecture?
In the architectural field, 3D scanning plays a crucial role in ensuring that designs are both feasible and efficient. Traditional surveying methods can miss crucial details or introduce errors, but 3D scanning technology offers unparalleled accuracy. This technology is particularly valuable for restoring historical buildings or working on complex projects with intricate layouts. By utilizing 3D scans, architects can visualize designs more accurately and create detailed plans that translate seamlessly into real-world applications.
Moreover, 3D scanning is indispensable for retrofitting and renovations, where precise documentation of existing conditions is needed to avoid construction issues. As the design phase is streamlined, project delays are minimized, ensuring more efficient use of resources.
Factors That Affect 3D Scanning Cost
Several factors influence the cost of a 3D scanning project. Key variables include the size and complexity of the site or object being scanned, the level of detail required, and the geographical location of the project.
1. Size and Scale of the Project
Larger structures like stadiums, airports, or warehouses demand more time and resources to scan, leading to higher costs. On the other hand, smaller spaces with simpler layouts may be less expensive, as fewer data points need to be captured.
2. Project Complexity
If the site contains intricate architectural details, such as historical buildings with ornate facades, the scanning process becomes more challenging and time-consuming, increasing the overall cost. Even small projects can be costly if the structure is highly detailed or has many rooms and layers.
3. Turnaround Time
Urgency can also affect pricing. While most 3D scanning companies deliver results within a few days for simpler projects, fast-tracking more complex scans will require additional resources, thus inflating the price. This is particularly true for large-scale or international projects, where logistical considerations also come into play.
3D Scanning for Different Industries
Different industries have distinct requirements when it comes to 3D scanning, leading to price variations. For example, in the construction industry, scans may be used to verify measurements during the building process, thus reducing errors and construction time. Meanwhile, industries like entertainment or gaming may require highly detailed models for virtual recreations, which necessitates more advanced scanning techniques and increased costs.
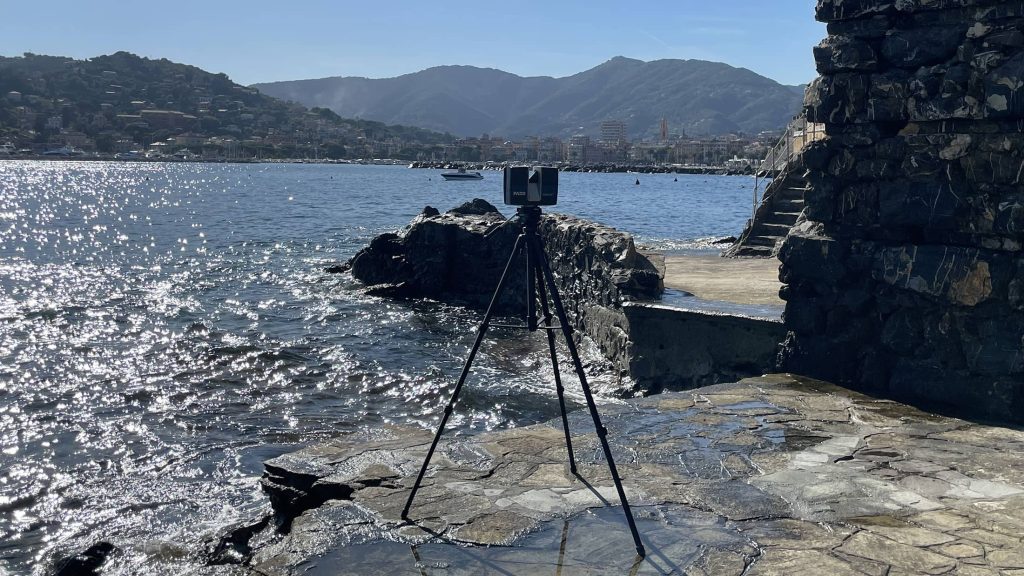
How 3D Scanning Benefits Large Construction Projects
Large construction projects often require high levels of accuracy to ensure that the plans are executable without incurring excessive rework costs. 3D scanning plays a vital role in verifying measurements and providing as-built models that reflect the actual conditions on site. This minimizes the chances of discrepancies between design and execution, saving companies both time and money.
For example, scanning an airport terminal before construction can reveal any potential issues with spatial alignment, allowing teams to make adjustments before work begins. This forward-thinking approach to problem-solving boosts efficiency while helping construction teams stay on budget by preventing costly revisions.
Cost Breakdown for 3D Scanning Projects
The cost of a 3D scanning project can vary greatly depending on the specific requirements. On average, pricing is calculated based on the size of the area being scanned, with most companies charging between $1.50 and $10 per square foot. However, the final price can also depend on factors such as the level of detail needed and the complexity of the scan.
For instance, scanning a small apartment with basic architectural features may cost around $500 to $3,000, whereas scanning a large stadium could range from $15,000 to $50,000 or more. Additionally, projects requiring advanced deliverables like point clouds, 3D models, and 2D drawings will have higher associated costs.
How the Size of the Project Influences
Price Large-scale projects like commercial buildings or industrial sites typically incur higher costs due to the amount of data that needs to be collected. More surface area means more time spent on-site and more complex post-processing. Smaller projects, such as residential homes or individual rooms, may be completed more quickly and, therefore, come with a lower price tag.
However, a small project with many detailed features could still drive up costs due to the complexity involved in capturing every aspect of the space. For example, scanning an intricate interior with multiple rooms and furniture requires more precision, leading to higher costs.
The Role of Complexity in 3D Scanning Pricing
Complexity is one of the most important factors that can significantly increase the cost of 3D scanning. For example, a simple rectangular warehouse will be much easier (and cheaper) to scan compared to an ornate historical building filled with intricate details. The more complex a structure is, the more data points the laser scanners must capture, and the more post-processing will be required to develop accurate models and point clouds.
When 3D scanning architectural monuments, cathedrals, or castles, for instance, the cost is often higher due to the level of precision needed to preserve even the smallest details. In such cases, specialized scanners, such as Leica or FARO, are required to ensure the highest accuracy, which can drive up the overall price.
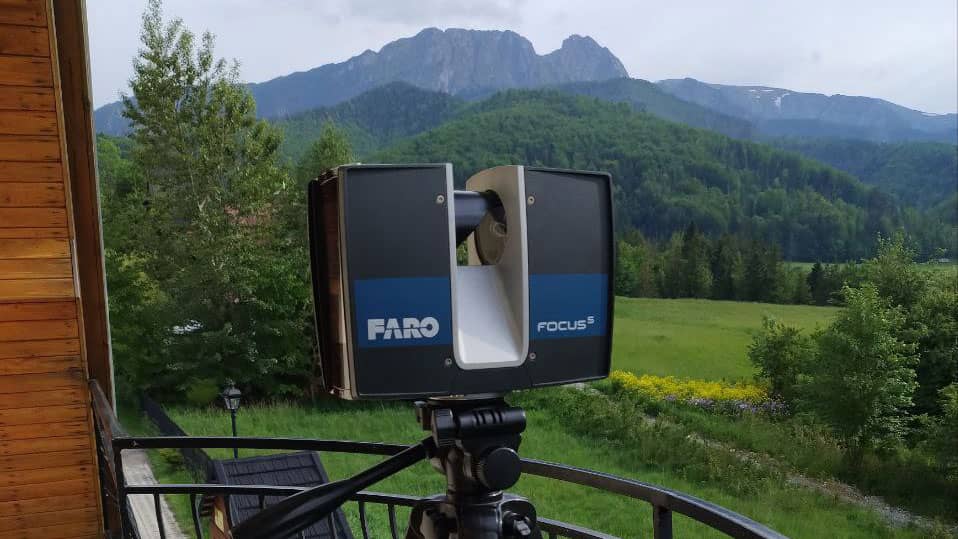
Time Frame for Completing a 3D Scanning Project
The timeline for delivering the results of a 3D scan varies depending on the size and complexity of the project. Smaller projects can often be completed within 1-2 days, while larger and more complex projects may take several weeks or even months. This time frame directly influences the final cost, especially when clients need faster delivery.
For example, scanning a simple office space may require just a few hours on-site, with the point cloud and 3D model delivered within 48 hours. However, scanning a sprawling industrial complex with complex machinery or a multi-story skyscraper will take longer, increasing both time and labor costs.
Geographical Location and Its Effect on Costs
While 3D scanning services are offered nationwide, the location of your project can influence the overall cost. In the U.S., projects located in major metropolitan areas, such as New York or Los Angeles, may come with higher prices due to the increased cost of doing business in those regions. Conversely, projects in smaller towns or rural areas may be more affordable, though clients might need to cover travel expenses for the scanning team.
For international projects, additional logistical factors like travel, accommodation, and transportation of equipment can significantly increase the cost. However, our company offers competitive pricing by covering a broad range of regions, minimizing travel expenses wherever possible.
Benefits of 3D Laser Scanning
The benefits of 3D laser scanning are vast, making it an essential tool across multiple industries. A key advantage is the unmatched precision it provides. With precision down to a millimeter, 3D scanning provides highly detailed data that ensures the success of architectural, engineering, and construction projects.
In addition to accuracy, 3D laser scanning significantly reduces the time needed to gather measurements. Conventional methods typically rely on manual measurements, which are not only time-consuming but also susceptible to human error. Laser scanning enables rapid capture of large structures, empowering project managers to make well-informed decisions with greater speed.
Lastly, 3D scanning is a cost-effective solution in the long run. While the initial scanning may come with an upfront cost, it can save time and money by reducing errors, rework, and material waste during the construction phase.
3D Scanning for Historical Preservation
Projects 3D scanning has proven to be an essential tool in the preservation of historical and cultural heritage sites. By creating highly accurate digital replicas, this technology allows for the restoration and maintenance of important landmarks without risking damage to the original structure. Additionally, it helps preserve these structures for future generations and can be utilized for educational initiatives or immersive virtual tours.
Although preserving historical monuments may require more intricate scanning techniques, the investment is invaluable for ensuring that these irreplaceable sites are protected. Historical scanning projects may cost more due to the level of detail needed, but the outcome is a detailed 3D model that can be used to restore or replicate the original structure with incredible accuracy.
Scan-to-BIM Services and Their Cost
Scan-to-BIM (Building Information Modeling) is a service that converts 3D scan data into usable BIM models. These models are essential for architects, engineers, and construction teams as they provide a detailed, digital representation of the physical structure. BIM models are instrumental in the planning, design, construction, and management of buildings and infrastructure.
The cost of Scan-to-BIM services depends on the complexity of the project and the level of detail required in the final model. For example, creating a detailed BIM model of a large commercial building can be more expensive due to the time it takes to convert the raw scan data into a structured, useful model.
Point Clouds and 3D Models: Deliverables Explained
One of the primary deliverables from a 3D scanning project is a point cloud, which consists of millions of data points representing the surfaces of the scanned object or space. From this point cloud, various outputs can be created, including 3D models, 2D CAD drawings, and building information models (BIM).
The choice of deliverable will depend on the client’s needs. For example, a construction company may require 2D drawings to aid in the building process, while an architect may prefer a detailed 3D model to visualize design changes. Delivering more advanced or processed outputs, such as a BIM model, typically involves more time and expertise, which can affect the overall cost.
Impact of Using High-Quality Scanners on Price
The quality of the equipment used for 3D scanning directly impacts the precision of the results and, consequently, the cost. High-end laser scanners like those from Leica, FARO, and Trimble are renowned for their accuracy and reliability. These scanners can capture data points at an extremely high resolution, ensuring that the final deliverables are of the highest quality.
While using top-of-the-line scanners may increase the price of the project, the added accuracy and efficiency often justify the higher cost. This is especially true for projects where precision is critical, such as engineering projects or the restoration of historical buildings.
How to Choose the Right 3D Scanning Service
Choosing the right 3D scanning service depends on several factors, including your budget, project timeline, and the level of detail required. When selecting service providers, it’s essential to assess their expertise, technology, and the quality of their previous projects. Opting for a company with a solid reputation for accuracy and reliability can help avoid costly mistakes later in the project.
It’s also important to evaluate if the provider offers adaptable pricing options, such as fixed rates or hourly billing. Depending on the project scope, one pricing model may prove more cost-efficient than the other.
Understanding the Value of 3D Scanning for Small Projects
While 3D scanning is often associated with large-scale industrial or commercial projects, it can also be highly beneficial for smaller projects. For instance, scanning a private home or a small office space can help architects and interior designers create more accurate floor plans and design layouts.
For small projects, the cost of 3D scanning is typically lower, especially if the space is simple and doesn’t require capturing extensive details. This makes it an appealing choice for homeowners planning a renovation or designers tackling residential projects.
3D Scanning for Reverse Engineering
In the fields of manufacturing and engineering, 3D scanning is frequently employed for reverse engineering, allowing for the recreation of a component or object from an existing physical model. This process is invaluable for industries that need to replicate components where no original drawings or plans are available. The scan captures every aspect of the part, allowing engineers to create an exact digital replica.
Although reverse engineering projects may be more expensive due to the complexity of the objects being scanned, the end result is a highly accurate model that can be used for manufacturing or further development.
How Accuracy Affects 3D Scanning Prices
The level of accuracy required for a 3D scanning project has a direct influence on the overall cost. High-precision scans that capture details down to the millimeter are more expensive due to the advanced technology and processing time involved. Such accuracy is crucial for engineering projects, where even the slightest discrepancies can cause major problems during the production or construction phases.
For projects that do not require such high levels of accuracy, more affordable scanning solutions may be available. It’s essential to consult with your 3D scanning provider about the required level of detail to strike the perfect balance between cost and quality.
Fast Turnaround: Is It Worth the Extra Cost?
When time is of the essence, clients may request expedited delivery of their 3D scanning results. While most projects can be completed within a standard timeframe, rush orders often require additional resources, leading to higher costs. In some cases, paying extra for faster turnaround times can be worthwhile, particularly if delays would disrupt the overall project schedule.
For example, a construction company on a tight deadline may find that paying for an expedited scan is a cost-effective solution, as it allows them to proceed with the project without incurring additional delays.
How Companies Offer Competitive 3D Scanning Pricing
Our company SCANM2 differentiates itself by offering highly competitive 3D scanning prices without compromising on quality. We accomplish this by blending streamlined scanning techniques, cutting-edge technology, and a client-focused approach. For example, we offer discounts on large-scale projects and can provide tailored pricing plans for smaller, more complex jobs.
Additionally, by using high-end equipment and experienced technicians, we ensure that the first scan is accurate, minimizing the need for costly rework. This enables us to provide highly accurate data at a cost that’s more competitive than many others in the industry.
Comparing 3D Scanning Prices Across Providers
When comparing 3D scanning prices across different providers, it’s important to consider not just the initial cost but also the value provided. Some companies may offer lower upfront prices but deliver less accurate or detailed results, leading to additional costs down the line. It’s essential to choose a provider that balances cost with quality, ensuring that the final deliverables meet your project’s needs.
Comparing reviews, checking past work, and asking for detailed quotes can help you make an informed decision.
The Future of 3D Scanning: Is It Becoming More Affordable?
As 3D scanning technology continues to advance, the cost of scanning services is expected to decrease. New developments in software and hardware are making the scanning process faster and more efficient, reducing the time and labor required to complete a project. Additionally, as more companies adopt 3D scanning for their projects, increased competition in the market is driving prices down.
While 3D scanning is still a significant investment for many businesses, it’s clear that the technology is becoming more accessible and cost-effective.
FAQ
What factors affect the cost of 3D scanning?
The cost is influenced by factors such as project size, complexity, location, and the level of detail needed.
How much does 3D scanning typically cost?
On average, 3D scanning costs between $1.50 and $10 per square foot, depending on the project’s specifics.
Can 3D scanning be used for small projects like homes?
Yes, 3D scanning is suitable for both large commercial buildings and small residential projects.
How long does it take to complete a 3D scanning project?
Simple projects can be completed in a few days, while more complex ones may take several weeks.
Does 3D scanning provide accurate measurements?
Yes, 3D scanning can capture measurements with millimeter-level accuracy, ensuring precise data for architectural and engineering purposes.
Is fast delivery available for 3D scanning projects?
Yes, but rush orders may incur additional costs due to the need for expedited processing.
Understanding the cost of 3D scanning is crucial for architects, engineers, construction companies, and private individuals planning to use this technology. While the price can vary depending on the size, complexity, and location of the project, the benefits of using accurate, efficient, and detailed 3D scans far outweigh the costs. As technology continues to evolve, 3D scanning is becoming more affordable, making it a valuable tool for a wide range of industries.