How Laser 3D Scanning Enhances Building Inspections
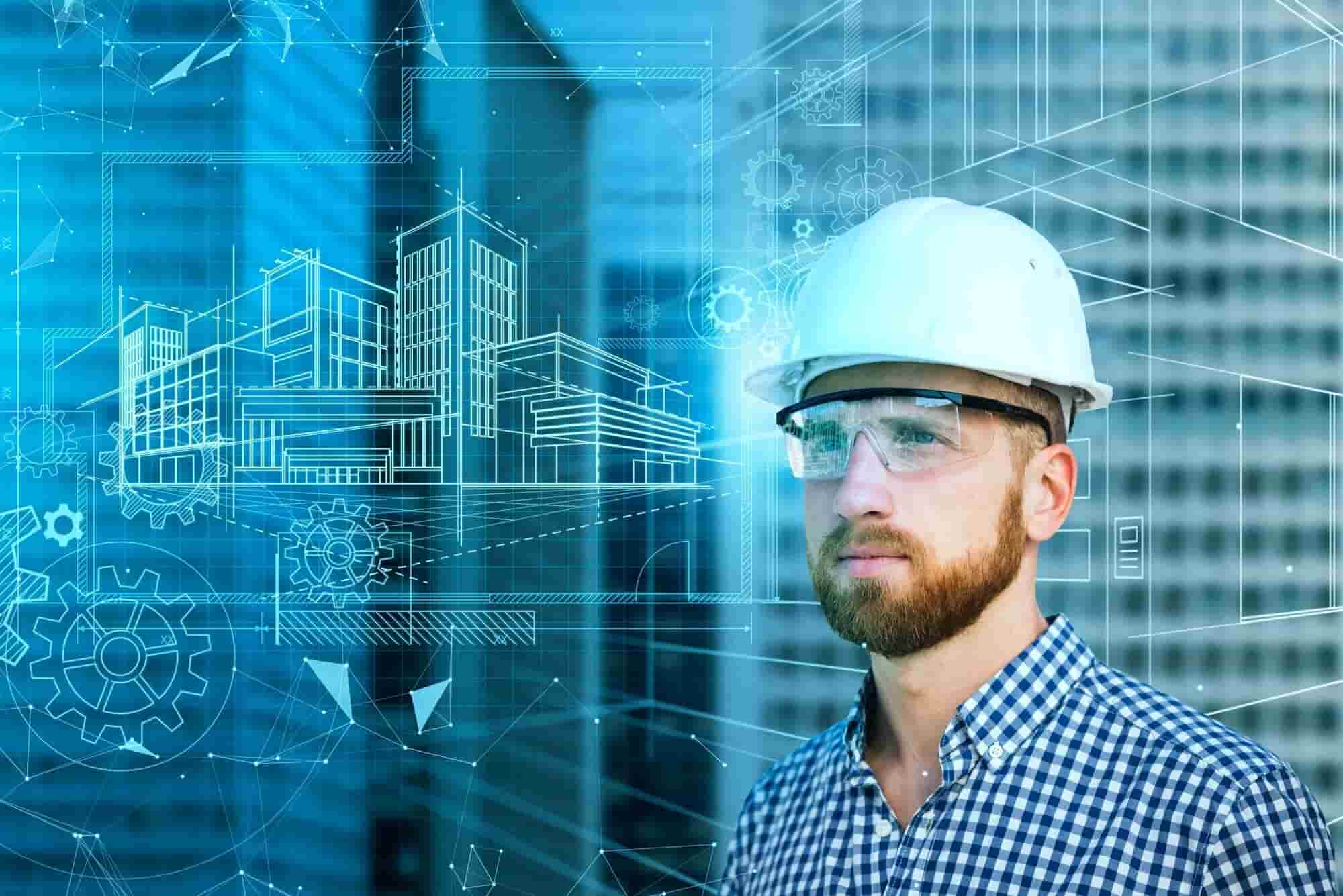
Building inspections have always been a cornerstone of the construction and maintenance industries. Ensuring the safety, compliance, and integrity of a structure requires accurate data and detailed analysis. The introduction of laser 3D scanning has elevated inspections to an unprecedented level of accuracy and effectiveness. This advanced technology allows inspectors and construction professionals to obtain highly accurate measurements and detailed visualizations of buildings, revolutionizing traditional methods.
In this article, we’ll explore how laser 3D scanning technology is transforming building inspections, its practical applications, and the benefits it offers to the construction and real estate sectors.
Understanding Laser 3D Scanning
Laser 3D scanning is a sophisticated technology that uses laser beams to precisely capture measurements of objects and their environments. The captured measurements are transformed into a point cloud, a digital format that creates an accurate 3D representation of the scanned space. This allows for highly detailed visualizations and comprehensive data that surpass traditional inspection methods.
Unlike manual measurements or visual inspections, laser scanning captures every surface detail with unmatched accuracy. This technology has become indispensable for analyzing construction sites and performing various inspection tasks.
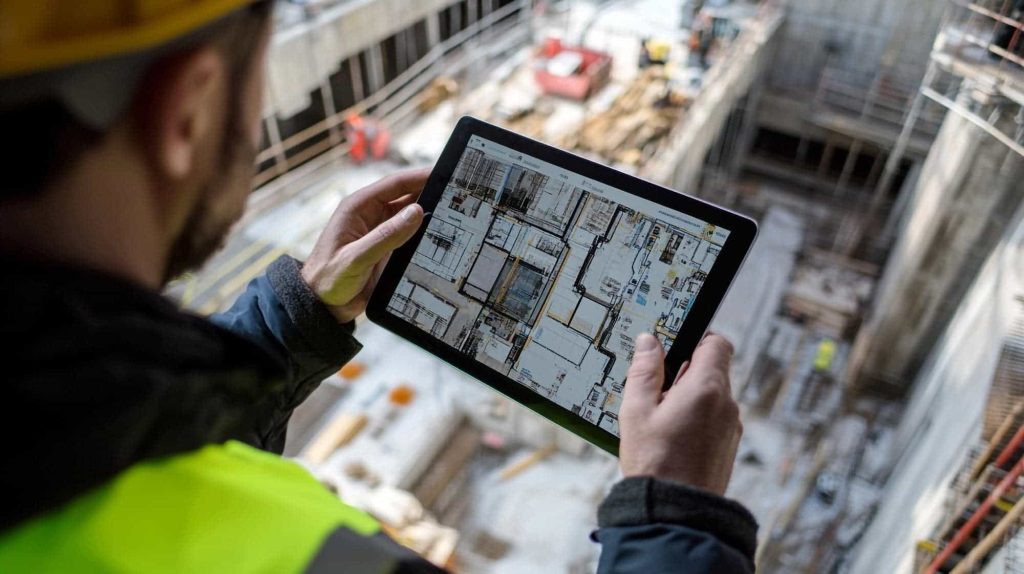
Key Benefits of Laser 3D Scanning for Building Inspections
1. Precision and Accuracy
A key benefit of laser 3D scanning lies in its capability to deliver highly accurate measurements.This level of accuracy is especially crucial in building inspections, as even small errors can result in expensive repairs or significant safety hazards. The technology ensures that every corner, beam, and surface is accounted for, leaving no room for guesswork.
2. Improved Safety
Inspecting buildings often involves accessing hard-to-reach areas, which can pose safety risks. With laser scanning for inspections, professionals can capture data from a distance, minimizing the need for scaffolding, ladders, or hazardous maneuvers. This enhances safety while also significantly shortening the time required for inspections.
3. Comprehensive Documentation
The data generated by 3D scanning is stored digitally, providing a permanent record of the building’s condition at the time of inspection. This can be invaluable for future reference, renovation planning, or legal documentation.
4. Time and Cost Efficiency
Conventional inspection methods typically demand considerable time and labor resources. Laser 3D scanning simplifies the process by collecting detailed data in significantly less time. This increased efficiency leads to lower labor expenses and accelerated project schedules.
Applications of Laser 3D Scanning in Building Inspections
- Structural Integrity Assessments: Inspectors use laser scanning to evaluate the structural soundness of buildings. Accurate models can reveal cracks, deformations, or structural weaknesses that might otherwise go unnoticed by the naked eye.
- Preserving Historical Buildings: For aging structures and historical landmarks, laser scanning offers a non-invasive method to thoroughly document and evaluate their current condition. These comprehensive insights aid in preservation efforts and ensure the structural integrity of historical buildings is upheld.
- Construction Progress Monitoring: Laser scanning is not limited to post-construction inspections. It’s also used to track progress on active construction sites, ensuring that work aligns with design specifications.
- HVAC and Utility Inspections: Laser 3D scanning is particularly useful for inspecting mechanical systems, plumbing, and electrical installations in buildings. Accurate models facilitate detailed assessments and enable early detection of potential issues, preventing them from developing into significant problems.
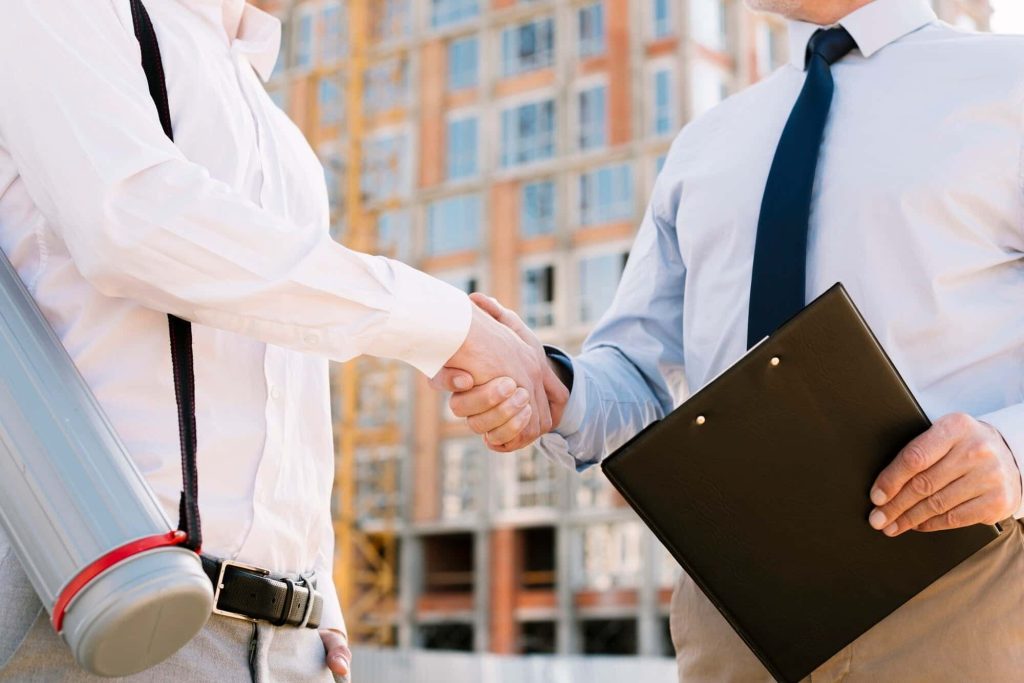
How Laser 3D Scanning Revolutionizes Traditional Inspections
Enhanced Visualization with 3D Models
Laser scanning’s ability to generate lifelike 3D models allows inspectors and stakeholders to explore every aspect of a building remotely. These models capture intricate details, such as walls, piping, and structural elements, enabling easier problem detection and collaborative solutions. Architects and technicians can also use these models for virtual walkthroughs and maintenance planning, saving time and resources.
Integration with Advanced Tools
Laser 3D scanning integrates seamlessly with Building Information Modeling (BIM) and CAD software, allowing professionals to compare current conditions with design plans and identify deviations accurately. Such integrations enable predictive analysis, aiding in the prevention of future structural or environmental problems.
Identifying Hidden Problems
Traditional inspection methods often overlook hidden issues. Laser scanning captures millions of data points to reveal anomalies like uneven surfaces, corrosion, or moisture infiltration. This precision makes it invaluable for inspecting facilities where minor issues can lead to major disruptions.
Why Businesses Should Embrace Laser 3D Scanning
- Improved Operational Efficiency: Laser 3D scanning drastically reduces inspection times, allowing businesses to optimize resource utilization more effectively. Inspections that previously required days can now be finished in hours, greatly enhancing overall project efficiency.
- Meeting Regulatory Standards: Accurate data collected through laser scanning ensures compliance with U.S. building codes and safety regulations. The detailed reports generated from scans provide reliable documentation for inspections, renovations, or maintenance.
- Competitive Advantage: Adopting laser scanning technology helps businesses stand out by offering precise services and faster project turnarounds. Real estate developers can showcase properties with 3D walkthroughs, while contractors can provide transparent updates, building trust with clients.
- Future-Proofing Investments: Laser 3D scanning prepares businesses for the future of the construction and real estate industries. Adopting this technology allows companies to stay ahead of market trends, securing long-term relevance and fostering innovation.
Final Thoughts
Laser 3D scanning goes beyond being a technological innovation—it marks a pivotal change in the approach to building inspections and construction projects. Its ability to deliver precise data, streamline operations, and enhance safety has made it a cornerstone of modern inspection practices.
For businesses, implementing this technology is a strategic step to stay competitive in a rapidly changing market. It facilitates improved collaboration between architects, engineers, and inspectors, ensuring projects are carried out with precision and efficiency. Investing in laser scanning improves current operations while positioning companies as forward-thinking leaders equipped to address future challenges.
Moreover, the versatility of laser 3D scanning extends beyond inspections. It plays a critical role in renovations, historical preservation, and even disaster recovery efforts, offering solutions that traditional methods cannot achieve. This adaptability ensures that the technology will remain valuable across various applications, making it a worthwhile investment for businesses of all sizes.
In an era where precision, speed, and innovation are paramount, laser 3D scanning stands out as a game-changing tool. By embracing this technology, U.S. businesses can unlock new possibilities, reduce risks, and achieve long-term success in the construction and real estate industries. Now is the time to leverage the power of laser 3D scanning and secure a competitive edge in today’s fast-paced world.