When Should You Upgrade from Manual Measurements to 3D Scanning?
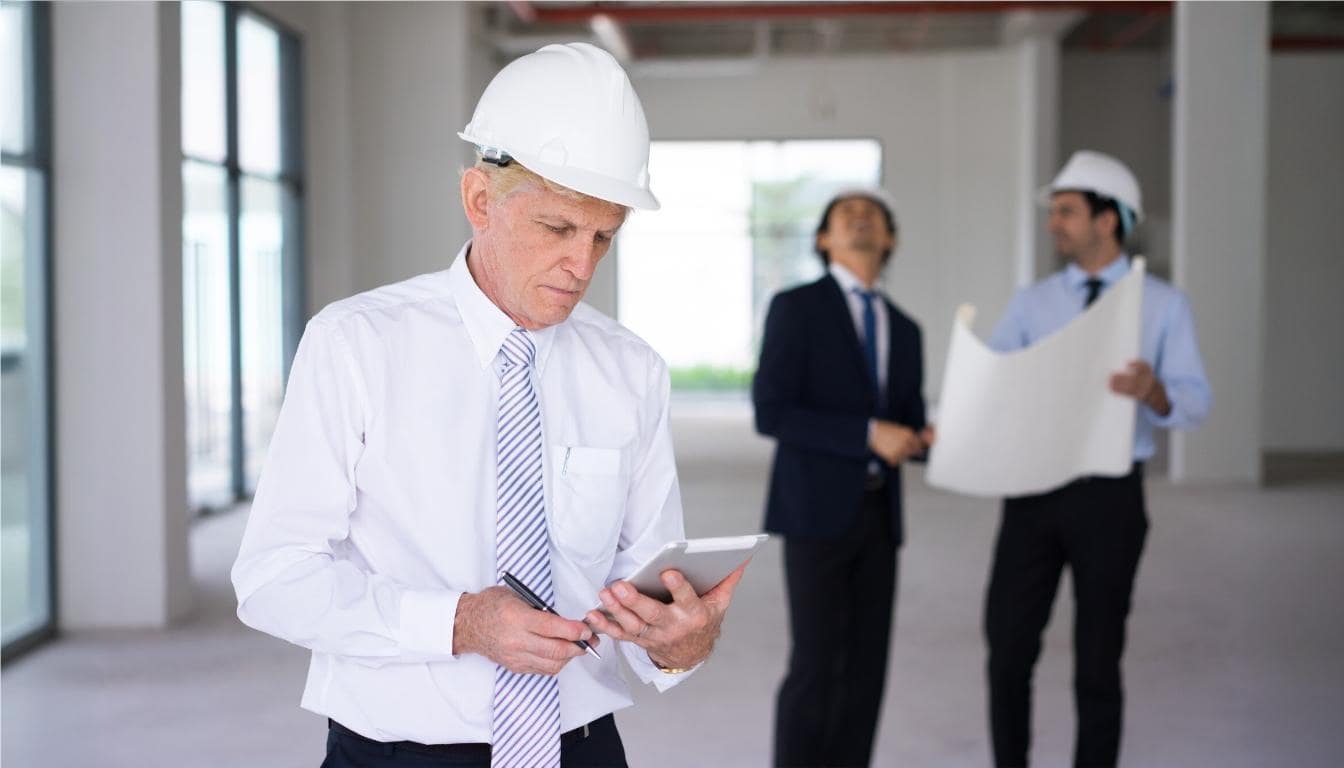
In construction, design, and renovation, even the smallest details play a crucial role. Accurate measurements are typically the foundational and most essential step for a project’s success. Traditionally, these measurements were taken manually, using tape measures, levels, and rulers. But as technology advances and projects grow in complexity, the limitations of manual methods become more apparent.
If you’ve ever faced challenges like inconsistent measurements, overlooked details, or the need to revisit a site multiple times, you might wonder if there’s a better way. Enter 3D laser scanning—a game-changing technology that’s transforming the way we capture and work with spatial data. So, when is the ideal moment to transition from manual measurements to 3D scanning? Let’s dive in.
Understanding the Increasing Complexity of Modern Projects
Modern construction and renovation projects often require a level of precision that manual measurements struggle to deliver. Picture this: a building with intricate architectural details, a factory with a maze of pipes and equipment, or a historic landmark with irregular shapes and angles. Manually recording these details is not only labor-intensive but also susceptible to mistakes.
This is where 3D scanning technology becomes indispensable. Using advanced lasers, scanners can quickly capture millions of data points, creating a highly accurate digital model of the space. This data can then be used for everything from designing renovations to solving complex engineering challenges.
But why not stick with the old ways? After all, they’ve worked for decades, right? Let’s delve deeper.
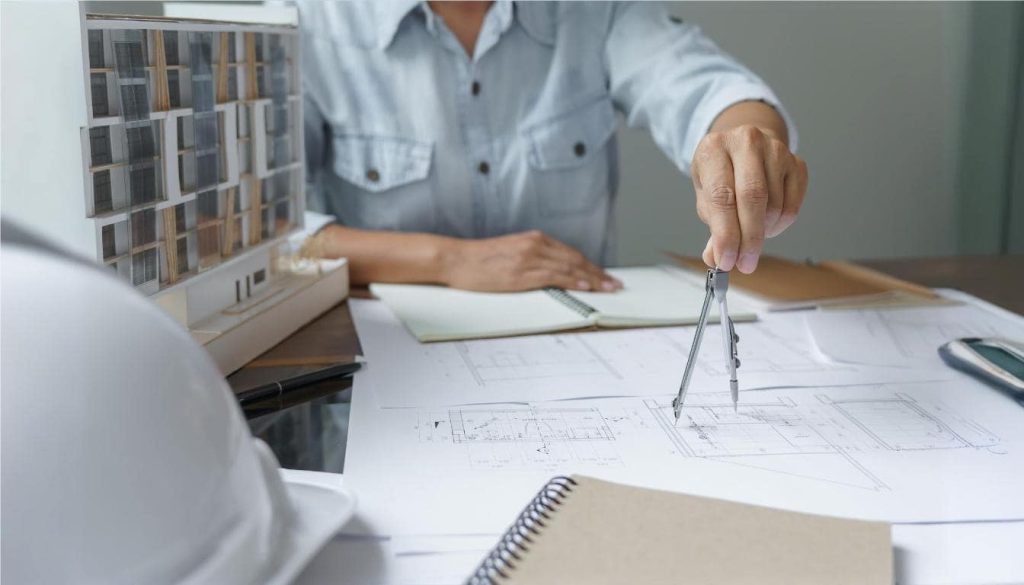
Why Manual Measurements Fall Short
Manual measurement techniques rely heavily on human effort and judgment. While experienced professionals can achieve reasonable accuracy, even the best teams can’t avoid occasional mistakes. A small misstep in measuring a doorway, ceiling height, or wall angle can lead to big problems later—delays, rework, and added costs.
Moreover, traditional methods often require multiple site visits. Imagine realizing halfway through a project that a key measurement was missed. You’d need to pause everything, send someone back to the site, and hope the new data integrates smoothly with your existing plans.
3D laser scanning, on the other hand, captures a complete snapshot of the space in one go. This means you have all the data you need from the start, including details you might not think to measure manually. Once you’ve worked with this level of precision, it’s hard to go back.
How 3D Scanning Works
For those unfamiliar, 3D laser scanning involves using a device that emits laser beams to map the dimensions and features of a space. As the laser hits surfaces, it collects millions of data points, creating what’s known as a “point cloud.” The point cloud can be transformed into a digital 3D model or seamlessly integrated into design tools such as AutoCAD or Revit.
The process is fast, precise, and incredibly detailed. In just a few hours, you can scan an entire building, capturing everything from structural elements to minute imperfections. This digital record can then be referenced throughout the project, ensuring everyone involved has access to the same accurate information.
When Should You Make the Switch?
The decision to adopt 3D scanning technology depends on your specific needs, but here are some signs that it might be time:
- Your Projects Are Getting More Complex: If you’re working on buildings with unique shapes, tight tolerances, or dense equipment layouts, manual measurements might not be up to the task.
- You’re Experiencing Frequent Errors: Do mistakes in measurements lead to costly delays or rework? Upgrading to 3D scanning can help eliminate these frustrations.
- Your Clients Expect More: As client demands for accuracy and transparency increase, being able to offer detailed 3D documentation can set you apart.
- You’re Adopting Digital Tools: Many industries are moving toward digital workflows like BIM (Building Information Modeling). 3D scans provide the precise input needed for these systems.
While these points offer guidance, the most compelling reason to switch often comes down to one thing: efficiency. In a competitive industry, saving time without compromising quality can make all the difference.
The Human Side of 3D Scanning
One of the most underrated benefits of 3D laser scanning is the sense of confidence it provides. Knowing that you have a complete, accurate digital record of your project removes much of the guesswork from design and planning. It allows you to focus on creative solutions instead of worrying about whether your measurements will hold up.
Clients, too, appreciate this level of precision. When you can share a detailed 3D model with them, it builds trust and opens up new opportunities for collaboration. Whether it’s a property owner seeing their renovation plans in stunning detail or a developer visualizing how new elements will fit into an existing structure, the impact is tangible.
Our 3D Models Examples
Overcoming Common Concerns
For some, the idea of adopting a new technology like 3D scanning can be intimidating. What if the equipment is too expensive? What if the learning curve slows down your team? While these concerns are valid, they can be effectively addressed.
For those hesitant to invest in their own scanner, partnering with a professional 3D scanning service can be a great way to get started. This allows you to test the technology without a significant upfront cost. Moreover, numerous providers offer training and support to help teams adapt to the new workflows with ease.
Once you experience the benefits firsthand, the decision to fully embrace 3D scanning often feels like a no-brainer.
Looking Ahead
The future of construction and renovation is undeniably digital. With the ongoing evolution of tools like 3D laser scanning, they are set to become an integral part of how we design, construct, and manage our spaces. Those who have embraced this technology early are already enjoying its benefits, including accelerated project timelines, reduced errors, and enhanced client satisfaction.
So, is now the right moment for you to make the upgrade? If you’re ready to leave the frustrations of manual measurements behind and embrace a more efficient, accurate way of working, 3D scanning technology is waiting for you. It’s more than just a tool—it’s a smarter and more efficient approach to work.